Our company’s offer corresponds to the general directions in the field of environmental protection, but also uses the current market situation, with drastic rising prices and restrictions in the combustion of fossil fuels.
First of all, environmental protection!
For both newly built and existing boiler houses, from 2023 a new directive on emissions will apply, the European Union Directive, the so-called The MCP Directive limiting the emission of nitrogen oxides NOx to a level below 100 mgNOx/m3 of flue gas (for currently designed and newly constructed facilities). Emissions of nitrogen oxides are given particular importance in this directive. This is due to the fact that these oxides are of particular importance for the protection of the environment. They affect the so-called acid rain and the increasing so-called “Ozone hole”.
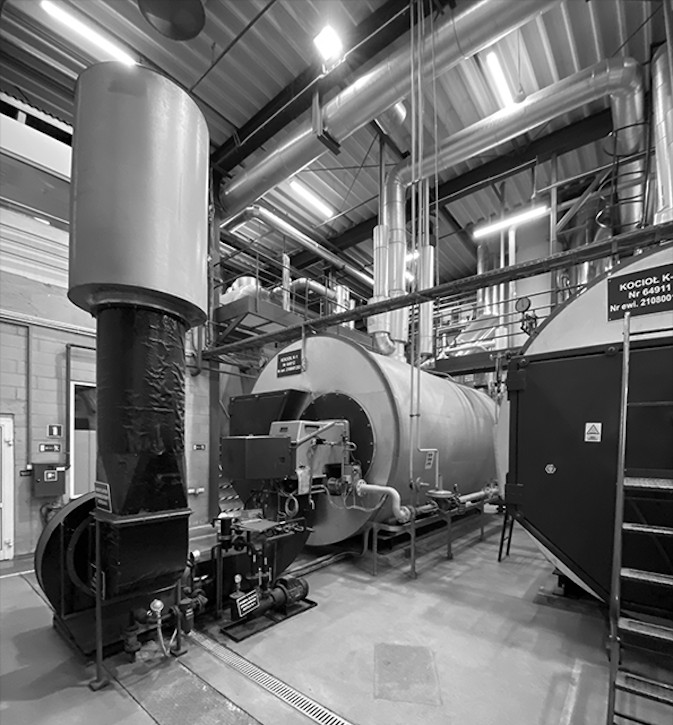
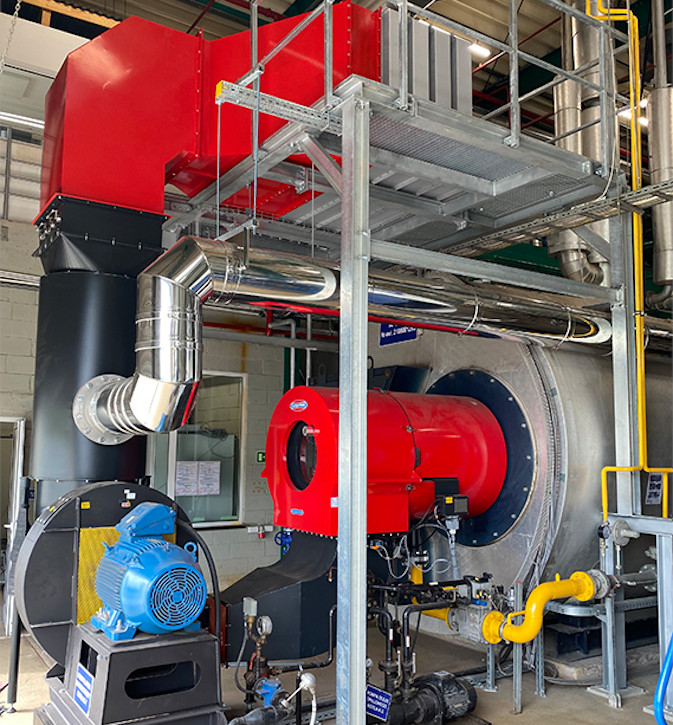

What does it mean? And the fact that out of a million exhaust particles only 48 particles can be nitrogen oxides.
Nitrogen oxides are formed in large quantities only due to the high temperature of the flame. The directive introduced the necessity of many new solutions, but also difficulties for both manufacturers of boilers and burners. The load intensity of the furnace chamber is one of the reasons for the increased formation of these oxides. The load intensity of the furnace chamber depends on the flame temperature, the size (diameter) of the furnace chamber, and the combustion air temperature. Some of the boiler manufacturers started the production of boilers with an enlarged flame tube (the space in which the burner flame burns). Of course, this increased the price of the boiler. For some burner manufacturers, it became impossible to obtain the expected parameters, for boilers with reduced dimensions of the furnace chamber.


Implementation of new facilities in the possibilities and modern solutions in the field of business and business operations of Limpsfield. Burners equipped with automatics and a supervision and supervision system for the auto-flame registration process.
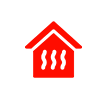
Implementation of heat recovery systems. In a steam boiler plant, for which the temperature of flue gases discharged to the atmosphere so far is often 160 – 180°C, thanks to the implementation of heat recovery systems, the norm is to discharge flue gases at a temperature of 60 – 70°C.

The implemented heat recovery systems enable: heating of feed water directed to the boiler, heating of combustion air to 130 ° C and heating of hot water for the needs of the plant (especially important in food industry enterprises).

Despite the introduction of heating of the combustion air, it is guaranteed that NOx emissions will be below the standards set by the MCP Directive.

We provide warranty and post-warranty service for all implemented and modernized facilities. For many years, we have been servicing boiler houses with thermal capacities from 2.5 MW to 60 MW.
We are an authorized representative of Autoflame and Limpsfield in Poland, whose devices ensure the maintenance of emissions at the appropriate level.
It is a manufacturer of burners that enable the combustion of natural gas, biogas, co-combustion of biogas with natural gas, light fuel oil, bioethanol, turpentine, hydrogen, animal fats, etc. With capacities from 0.4MW to 62 MW for one burner.

It is a producer of automatics, supervision and monitoring system of the combustion process.By using the products of both Limpsfield and Autoflame companies, we are able to guarantee the required emission levels for each modernization of existing boiler houses, both for boilers with more loaded flames and with air heating, emission effects difficult to achieve or not available for other manufacturers. It applies to both the implementation of new facilities and, what is particularly worth emphasizing, the modernization of the existing boiler houses. Boiler houses built 20-25 years ago often have fully valuable boilers. However, both the automatics and the conditions of fuel combustion in old burners do not guarantee the required emissions. There is often a lack of spare parts for burners that were produced over 20 years ago. The optimal solution is the modernization of such a boiler room based on burners and automation, allowing for emissions in accordance with the MCP Directive, but also increasing efficiency and obtaining significant savings in terms of heat production costs.
Synergy effect
By using the products of both Limpsfield and Autoflame companies, we are able to guarantee the required emission levels for each modernization of existing boiler houses, both for boilers with more loaded flames and with air heating, emission effects difficult to achieve or not achievable for other manufacturers. It applies to both the construction of new facilities, and, what is especially worth emphasizing, the modernization of the existing boiler houses. Boiler houses built 20-25 years ago often have fully valuable boilers. However, both the automatics and the conditions of fuel combustion in old burners do not guarantee the required emissions. There is often a lack of spare parts for burners manufactured more than 20 years ago.
Lowering the cost of heat production, rationalizing heat management.
With the use of modernization, it is possible to reduce fuel consumption by up to 10% and thus reduce operating costs.
Boiler rooms equipped with “traditional” burners manufactured 20 – 25 years ago are often characterized by a combustion process with 5 – 6% O2 content in the flue gas. Burner adjustment is usually performed twice a year and sometimes less frequently. This alone causes significant losses due to ineffective fuel combustion.
Our proposed burners and supervision system ensure the combustion process with the oxygen content in the exhaust gases below 3%. The continuous monitoring system of the combustion process guarantees not only keeping the O2 content below 3%, but also “adjustment” of the combustion process with variable parameters such as atmospheric pressure, combustion air temperature, variable calorific value, for example in the case of biogas.
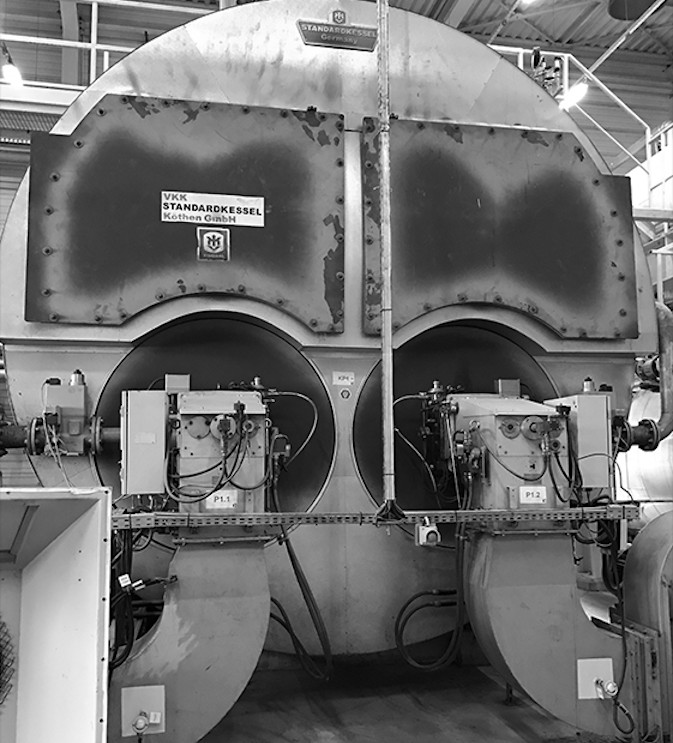
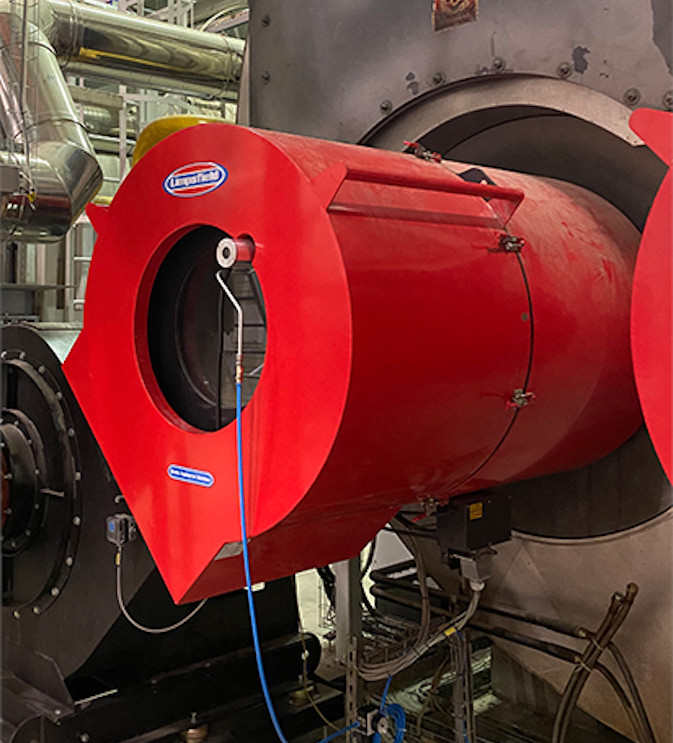